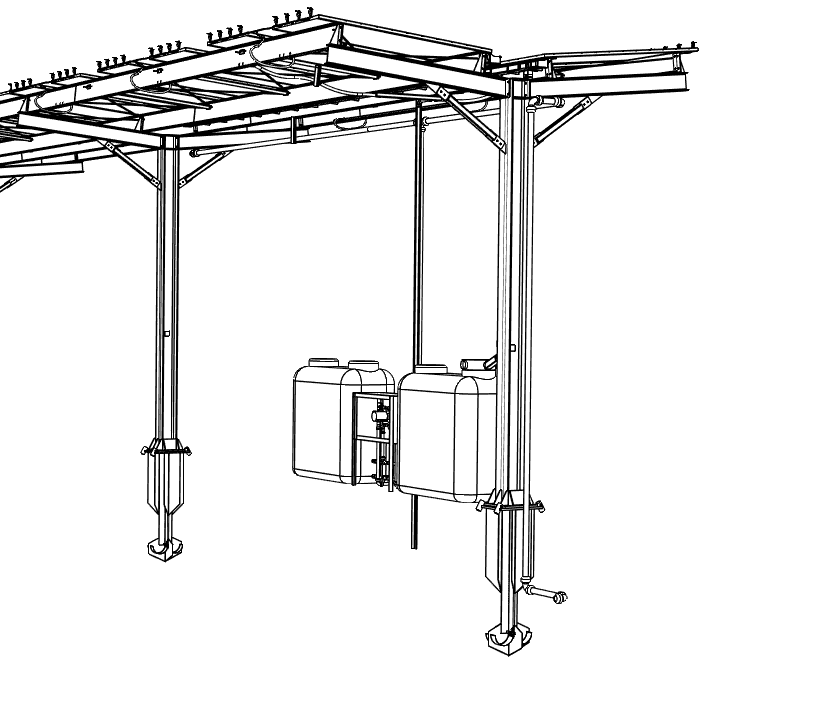
This is a new design for solar cell power conducting design. Instead of stripes as in MBB or SMBB technology, ZBB has very tiny wires for transferring energy into cells and between cells. The simple way explanation for ZBB is the smallest interconnection at the solar cell that is better for the performance and strength of cell.
Overall, SMBB and ZBB technology represents a significant step forward in solar cell design, helping to improve photovoltaic systems’ performance, efficiency, and reliability, which are vital for the widespread adoption of renewable energy sources and combating climate change.
The HJT G12 solar cells are designed with a unique structure that combines monocrystalline silicon and thin amorphous silicon layers. This innovative design is intended to minimize electron recombination losses, thereby enhancing the overall efficiency of the cells and reducing energy loss during the conversion process. The G12 (210mm) cells are further equipped with BusBar technology, which provides several new advantages for heterojunction solar modules. Overall, the utilization of this advanced technology in the development of HJT G12 solar cells has significantly improved the performance and effectiveness of these solar modules.
These are the main features and qualities that can be associated with G12 HJT solar cells.
The HJT technology is one of the best in high-efficiency solar cells for the new generation. It leads the way in a new revolution in PV technology by integrating the advantages of crystalline silicon and amorphous silicon thin film technology into a single hybrid structure. The HJT solar cell has several advantages, including high efficiency, stability, and simplified manufacturing procedures, all while operating at low temperatures.
The HJT solar cell has an extremely low-temperature coefficient, which helps avoid LID and PID effects. Moreover, there is no color difference between the front and back sides, and the bifaciality is more than 95%. The backside of the solar cell has a significant power generation advantage, which ensures a stable and high-efficiency power output regardless of seasonal circulation and climate change.
MySolar a solar panel manufacturer, announced in 2023 that it has launched commercially available HJT + perovskite solar cells with a power output of 250 W. The company was founded in 2013 and has since become one of the leading solar panel manufacturers in Poland. HJT + perovskite cells are a new technology with the potential to revolutionize the solar industry.
MySolar a solar panel manufacturer, announced in 2023 that it has launched commercially available HJT + perovskite solar cells with a power output of 250 W. The company was founded in 2013 and has since become one of the leading solar panel manufacturers in Poland. HJT + perovskite cells are a new technology with the potential to revolutionize the solar industry.
Kapaciteti Srbije za PV Instalacije 1. Obilje pogodnog zemljišta: Srbija ima velike površine zemljišta pogodnog za fotonaponske (PV) instalacije. Topografija zemlje uključuje ravne ravnice, posebno
Serbian Land Capabilities for PV Installations 1. Abundance of Suitable Land:Serbia has vast expanses of land suitable for photovoltaic (PV) installations. The country’s topography includes
We will support you and help you achieve your solars goals. From project to installation, we can help you every step of the way. Join our family and own your solar investment. What are you waiting for? Take the first step today.
© 2021 All Rights Reserved. Privacy Policy Sitemap